2.2.3 Additional material on Propulsion
Course subject(s)
Module 2. Propulsion and Braking

As Bas discussed in the first video this week there are many different methods of propelling our Pod forwards. In this segment we will review the concepts that were discussed and have a more in-depth look.
Internal Combustion Engine
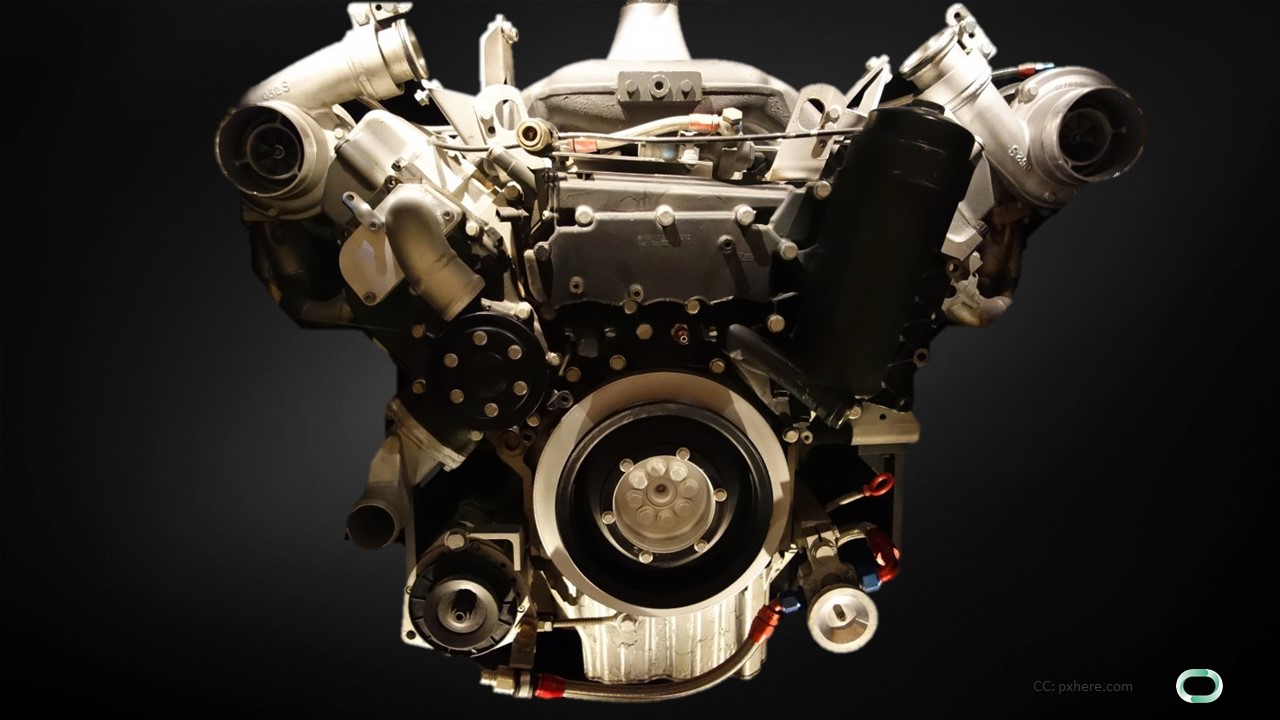
In the video lecture, we determined early on that the internal combustion engine is unsuitable for the Hyperloop concept. The first reason being that any combustion engine is incompatible with the vacuum environment as combustion requires oxygen. We could solve this by bringing it on board in a separate tank like they do with rockets. This, however, would result in an increased mass and hazard. The other reason why we consider it unsuitable is that combustion causes pollution and is there for fundamentally less environmentally friendly than the other options.
Electric rotation motor
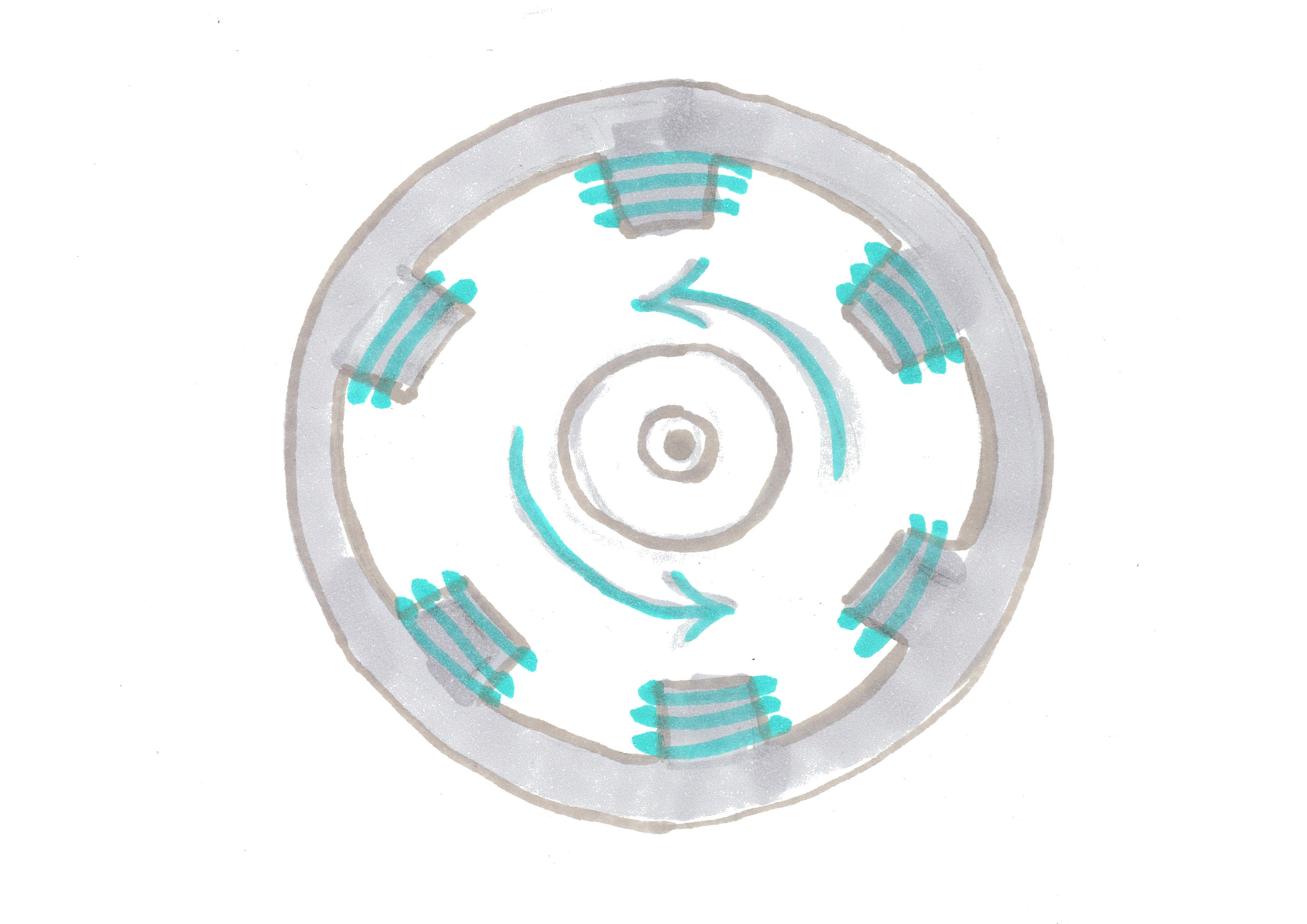
The electric motor is increasingly being implemented in the transport sector due to the rise of the electric car. However, this technology has already been put to use for more than a century in the electric train locomotive. The electric rotation motor has proven to offer great performance and reliability when converting its electrically stored energy into work. The other benefit is that this energy can be gathered from renewable sources like solar panels and windmills and therefore offers a more durable option. This type of motor was used by the second Delft Hyperloop team mainly for its great acceleration performance.
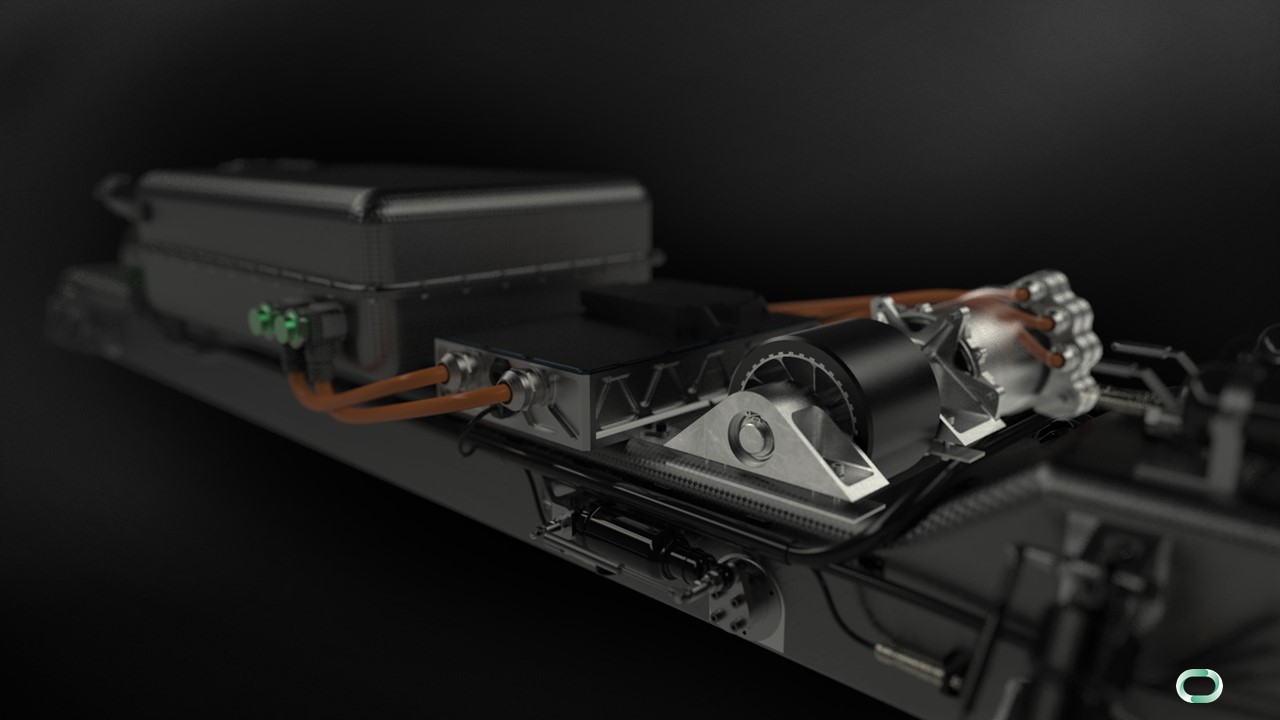
The downside of this motor, however, is the way we put the work to use and propel the Pod forward. The most likely option would be wheels as discussed in the previous week, however, we saw that wheels are very limiting to the top speed of our vehicle.
Another option is the use of Electro-Dynamic Wheels (EDWs); these have been implemented in the 2018 Pod of our friends over at UCSB Hyperloop who, like us, also competed in the SpaceX Hyperloop Competition. These wheels aren’t actually regular wheels but rather disks that are built up out of a magnetic array. By rotating these wheels over a conductor we get the same Electro-Dynamic Suspension effect as with the levitation, only we can hover the pod at standstill. By altering the arrangement of these wheels we can also use the magnetic drag the propel the Pod forwards. This method could be compared to a helicopter, however, we’re using magnetic lift instead of the aerodynamic lift. Unfortunately, similar to helicopters this method is also not that efficient and a great deal of its energy is lost by simply hovering as well as the magnetic end effects that occur.
Linear Induction Motor
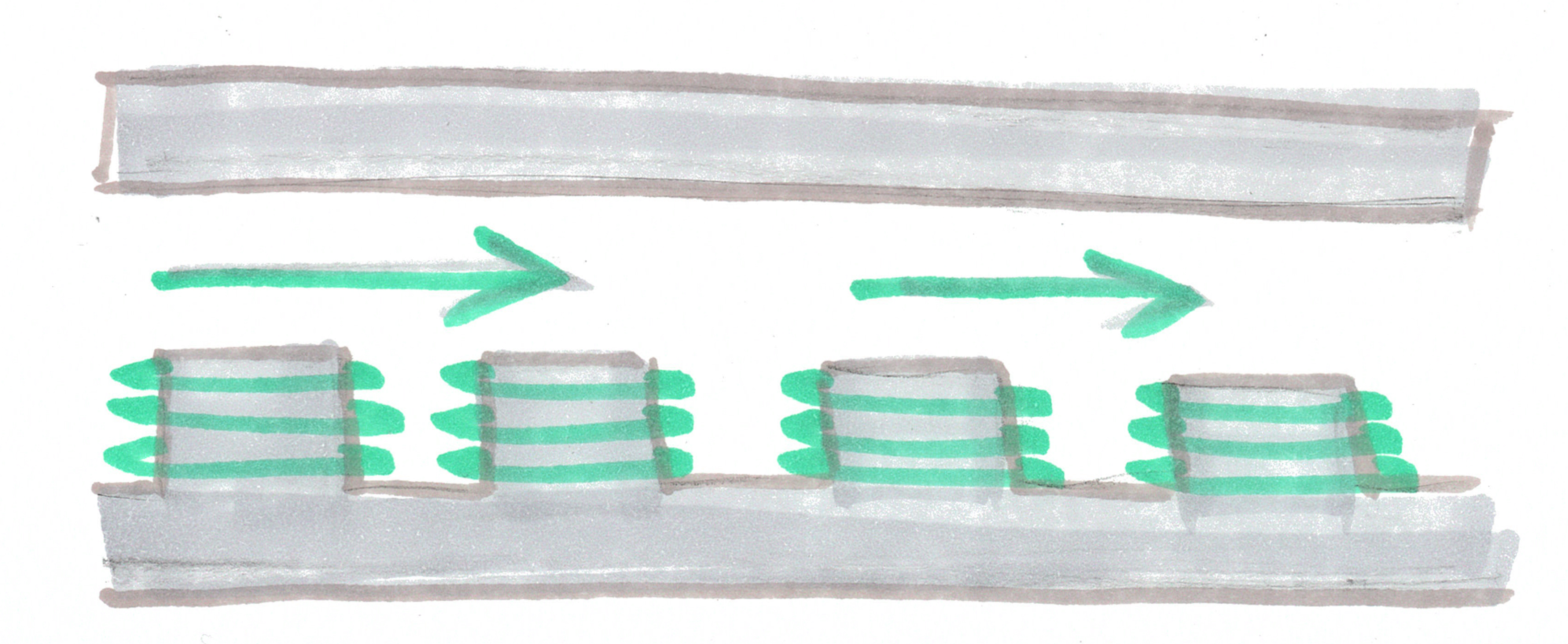
The linear induction motor is a relatively new concept, not widely implemented in current day use. They can be found in aircraft carrier launch systems as well as in some roller coasters. The stator and the rotor found in a rotational motor have been rolled out in a linear pattern. By inducing a magnetic wave in the rotor, the stator can ‘surf’ this wave and is propelled forwards. The big benefit of this is that it happens contactless and therefore it is not prone to wear. As discussed by Bas, there are different configurations among which are the Single-sided Linear Induction Motor (SLIM) and the Double-sided Linear Induction Motor (DLIM), where the use of a DLIM setup results in a decrease in the loss in the end effects of the magnetic fields. These types of motors are currently researched and implemented by the company Hyperloop One over at their Dev Loop in Nevada, some impressive videos of this can be found online.
Cold Gas Thruster
By storing a cold gas under high pressure and releasing it, there will be a reaction force according to the third law of Newton that propels us forwards. This concept is comparable to filling up a balloon and then releasing it. The major difference is that we need a rather large volume and a very high pressure for this to work. Thruster systems like these are used in satellites for attitude control because of the vacuum environment up in space. These systems need to be very heavy to work on a large vehicle like the Hyperloop, unfortunately. Another problem is that by releasing this gas we are filling up our tube and would need an increased amount of vacuum pumps to get rid of. Systems like this have been implemented to Hyperloop by the Swissloop team and the Washington State University Hyperloop team, both attempts, however, have proven to be very difficult and unfortunately led to less performance than expected.
Rockets
Rocket propulsion could be compared to the Cold Gas Thruster, however this time it is a Hot Gas that is exerted by combustion. This brings us the same problems that we’ve encountered in the other combustion engines. They are used in space launch systems for their unbelievably high thrust performance. The risk with Hyperloop, however, is that with these high temperatures we could damage the Tube, next to the problem of removing the combustion gasses.

Hyperloop: changing the Future of Transportation by TU Delft OpenCourseWare is licensed under a Creative Commons Attribution-NonCommercial-ShareAlike 4.0 International License.
Based on a work at https://online-learning.tudelft.nl/courses/hyperloop-changing-the-future-of-transportation/.