2.5.2 Case: Relight Italia
Course subject(s)
Module 2. Recycling
Case: Recovering rare earth metals from old TVs and lights
In this part of the module a description is given of a plant in Italy that recovers critical raw materials from old TVs and fluorescent lights. Due to the complexity of the waste flows, the overview is given by text and not by a video. An impression of the Relight plant and company is to be found in this online video.
Relight is an Italian recycling company based in the city of Rho in Northern Italy. The processing plant of Relight has an authorized capacity of 40.000 (metric) tons per year. Relight processes four different types of waste:
1. CRT TVs and monitors (the old big “tube” TVs)
2. LCDs
3. Electronic appliances
4. Fluorescent lamps
The fluorescent powder of the fluorescent lamps (also from the LCDs) and the CRT TVs and monitors are treated in a hydrometallurgical plant.
- CRT TVs and monitors
The CRT TVs and monitors are manually dismantled and the CRT “tube” is cut in half, so it falls open and the fluorescent powder inside can be vacuumed up. This powder is collected in the filter. The glass is cleaned in a glass refining plant, which delivers clean glass particles for recycling. The yokes and cables of the TVs and monitors are removed and after shredding, ferrous and non-ferrous metals and plastics are separated.
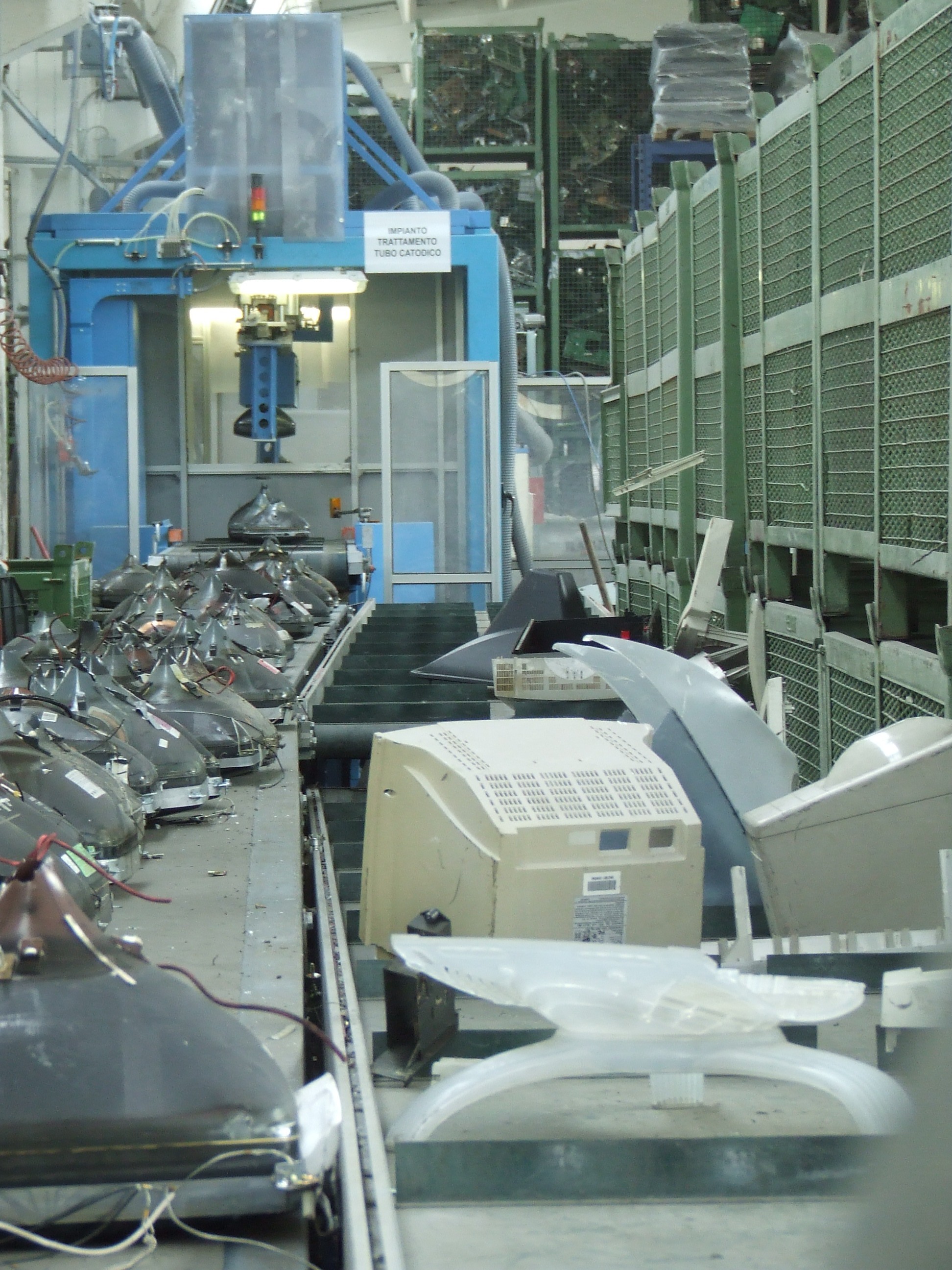
2. LCDs
The LCD-screens are also dismantled, into LCD-panels, PCBs, PMMA plastics, cables, fluorescent lamps and plastics. The fluorescent lamps are further processed in the dedicated line.
3. Electronic appliances
Electronic motors and PCBs are removed from electronic appliances. The rest is shredded and separated into plastics, and ferrous and non-ferrous metals.
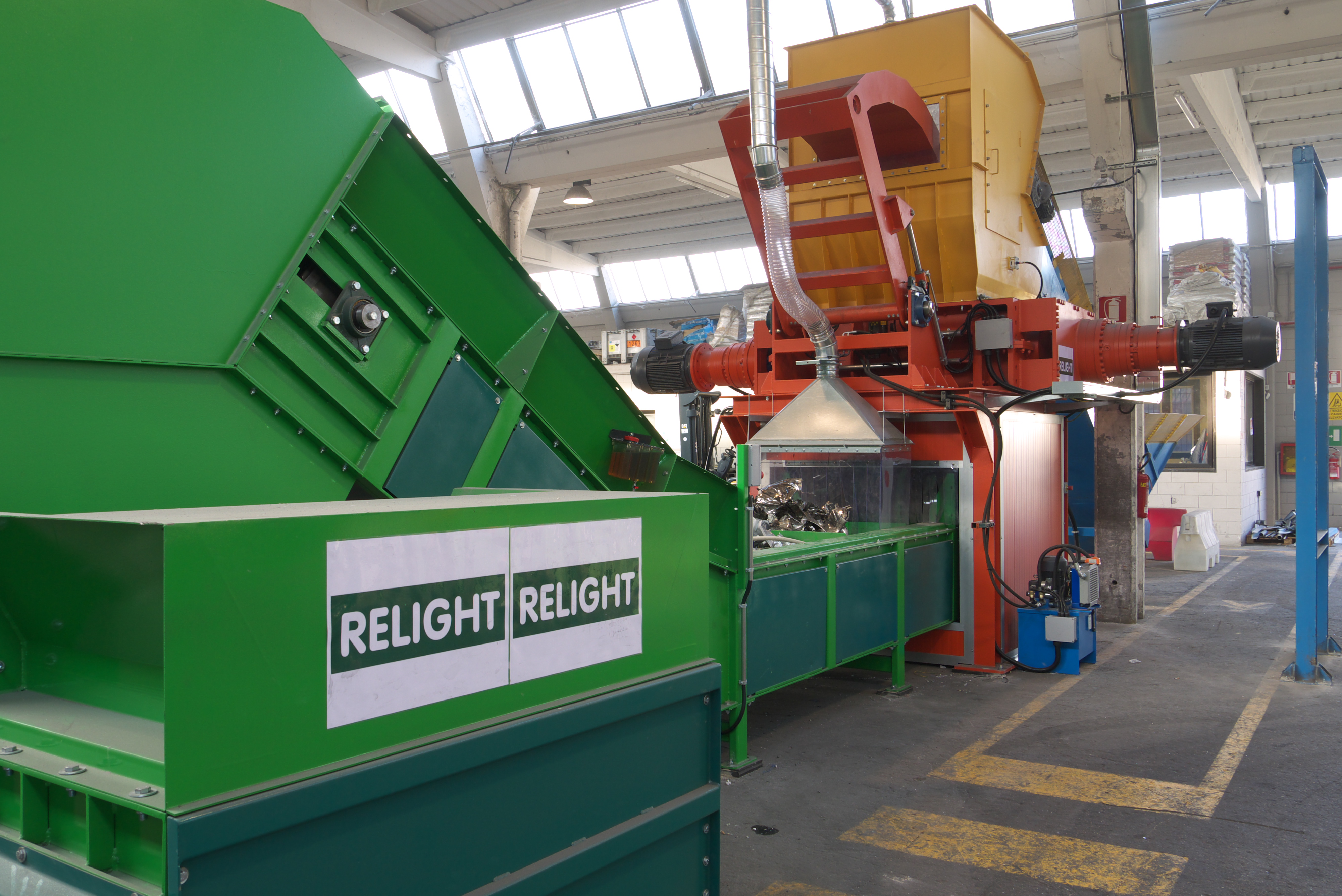
4. Fluorescent lamps
In the treatment of fluorescent lamps, the lamps are shredded, and separated into fluorescent powder, glass, and ferrous and non-ferrous metals.
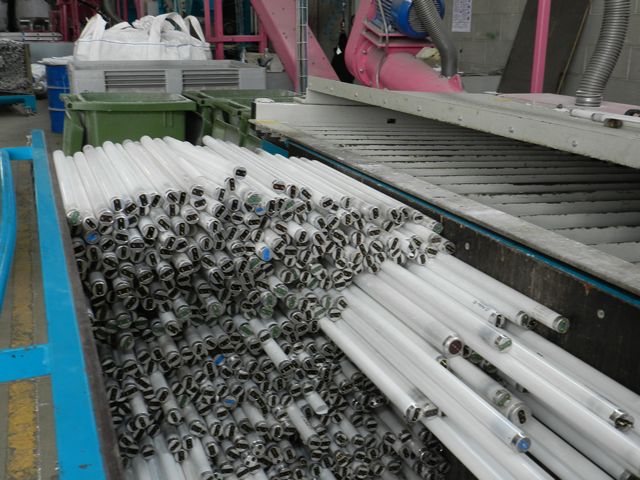
Different fractions
Yokes, cables, various ferrous and non-ferrous metals will be sent to foundries for the material recovery. Plastics are separated based on their density, for further processing by partners of Relight. Glass is used in the ceramic industry, for the production of tiles, amongst other.
Hydrometallurgical installation
From the fluorescent powder of the processes above, critical raw materials are recovered. These recovered critical raw materials are rare earth metals, and are, amongst others, Yttrium, Europium, Gadolinium and Terbium. The recovery takes place in a batch operated installation with a capacity of 600 kg per batch. The fluorescent powder is fed first to a hopper were more glass particles are removed. Then it is fed to a leaching reactor, where the reare earth metals are dissolved in a solution. In a filter press the leachate with the rare earth metals is squeezed from the first filtration. This rare earth metals containing leachate is sent to a second reactor where the rare earth elements are precipitated with an oxalic acid to a oxalate of rare earth elements. In a second filter press the precipitated rare earth metals oxalate is squeezed dry in a filter cake. The production is about 200 kg per batch, and that corresponds to about 165 tons per year. Waste water of the plant is treated with lime, and the water is reused in the process.
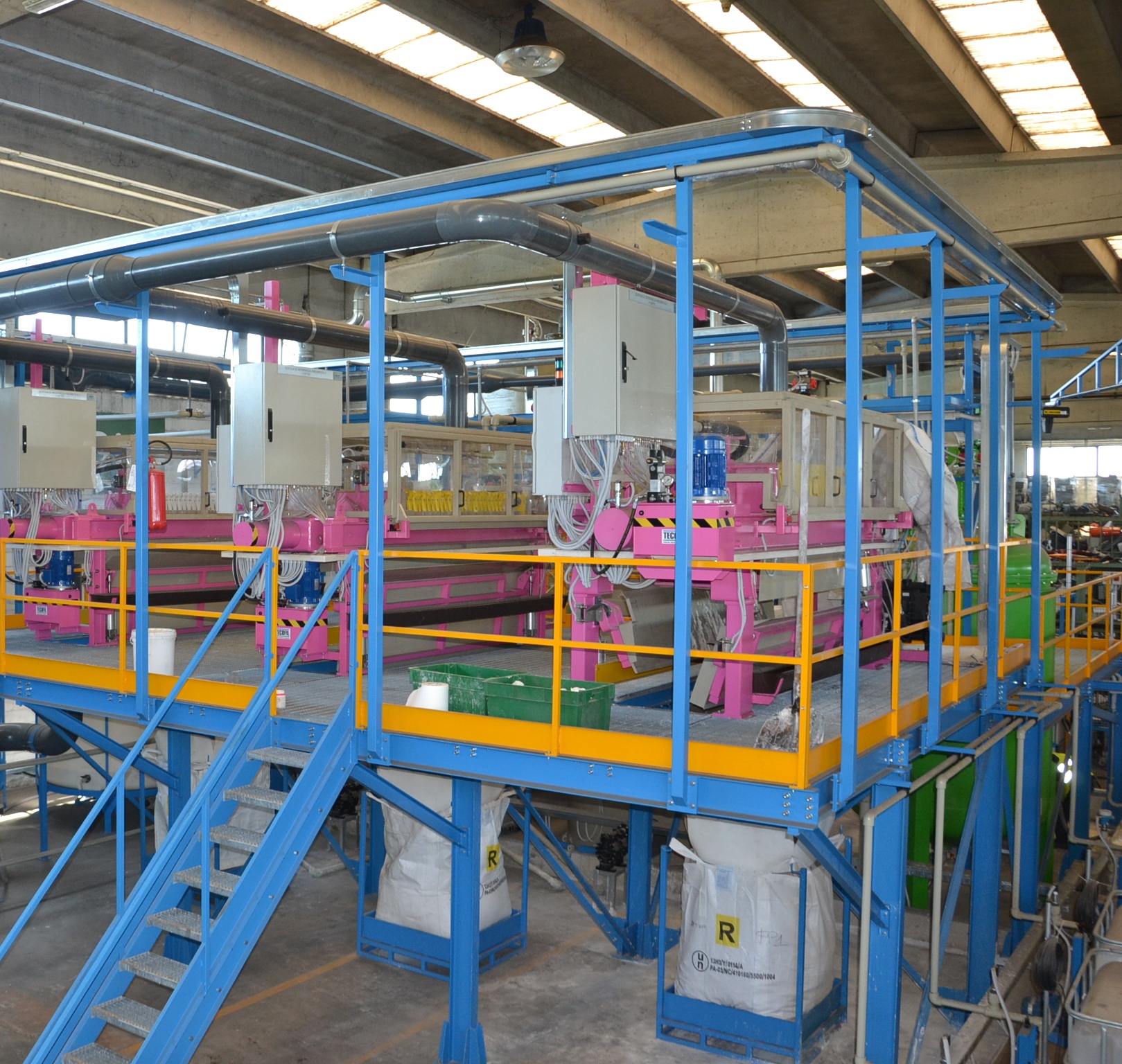
The hydrometallurgical installation
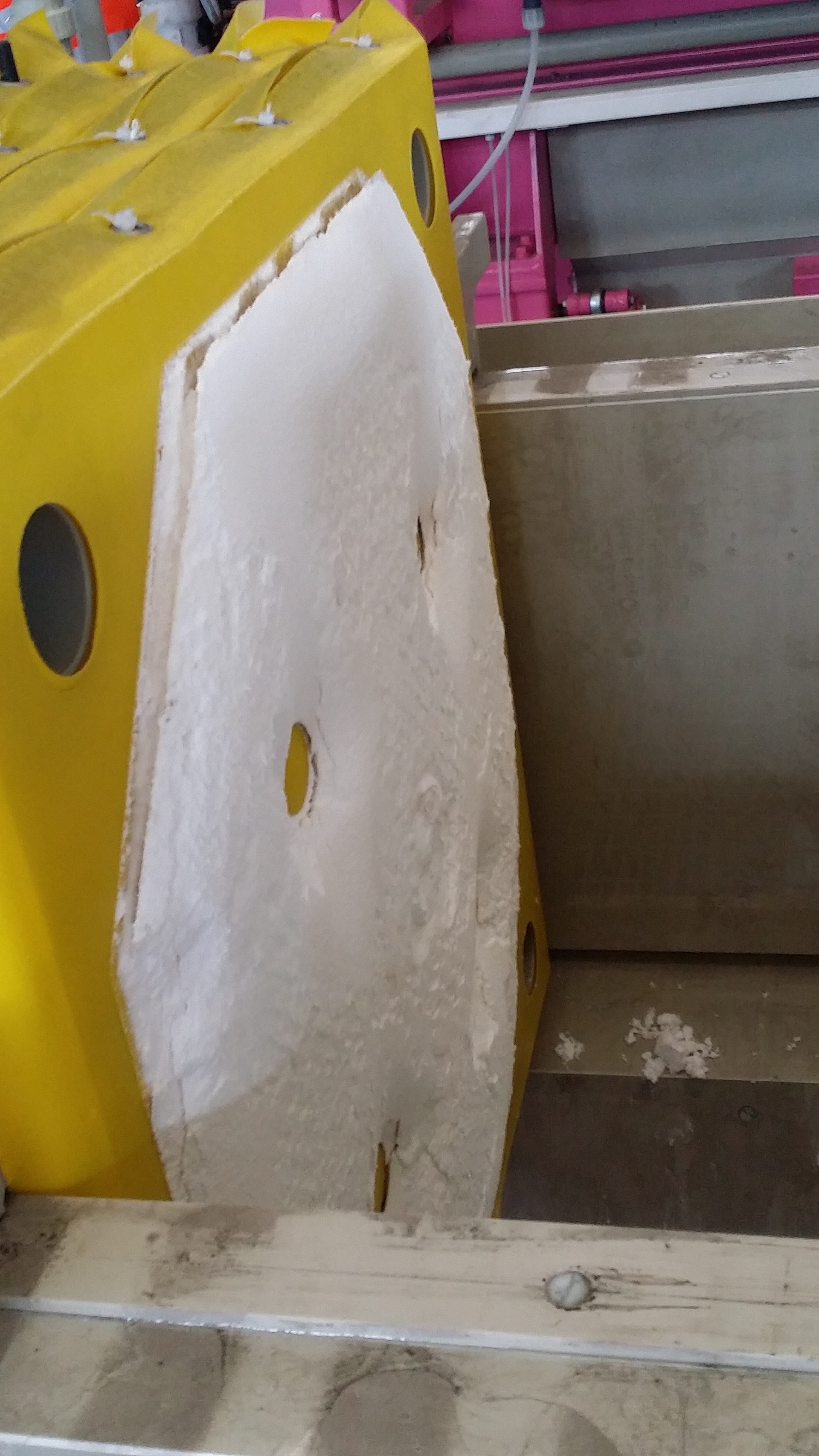
The metals Yttrium, Europium, Gadolinium and Terbium are part of the list of heavy rare earths, and this list is again part of the 27 raw materials that are critical for the EU (source “ the 2017 list of Critical Raw Materials for the EU”, Brussels, 13.9.2017 COM(2017) 490 final“)

Waste Management and Critical Raw Materials by TU Delft OpenCourseWare is licensed under a Creative Commons Attribution-NonCommercial-ShareAlike 4.0 International License.
Based on a work at https://online-learning.tudelft.nl/courses/waste-management-and-critical-raw-materials/.